.
Plasma cutting
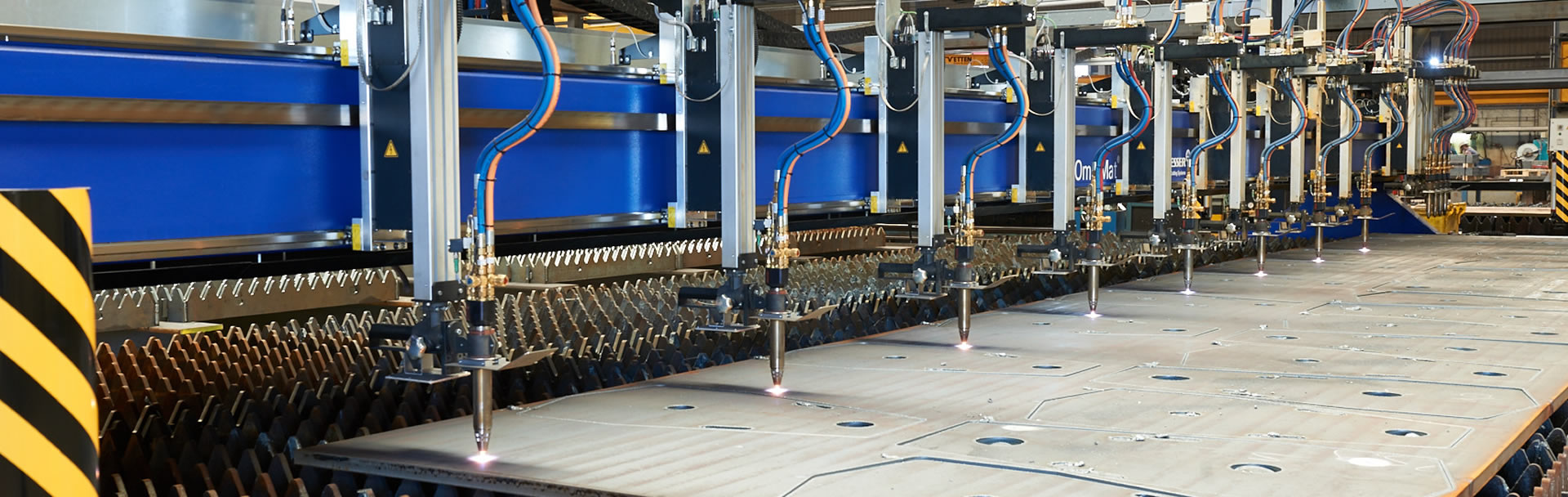
Flame cuts are the results of flame cutting. Flame cutting is a separation process in which metals and steels can be cut. Physically, the cutting process only works because metals and steels burn in pure oxygen. It is important that the combustion temperature is below the melting point of the material to be cut. The flame used consists of fuel gas and oxygen. This creates the flame joint or kerf. The nature of the kerf depends on the gas setting, the cutting speed and the cutting direction.
State-of-the-art cutting systems and our staff, who have many years of expertise, guarantee the delivery of above-average quality with short and reliable delivery times. Depending on the grade, thickness, dimensions, tolerance and quality requirements, we can produce material thicknesses of up to 600 mm on our CNC-controlled oxyfuel, plasma and laser cutting systems.
Oxyfuel flame cutting
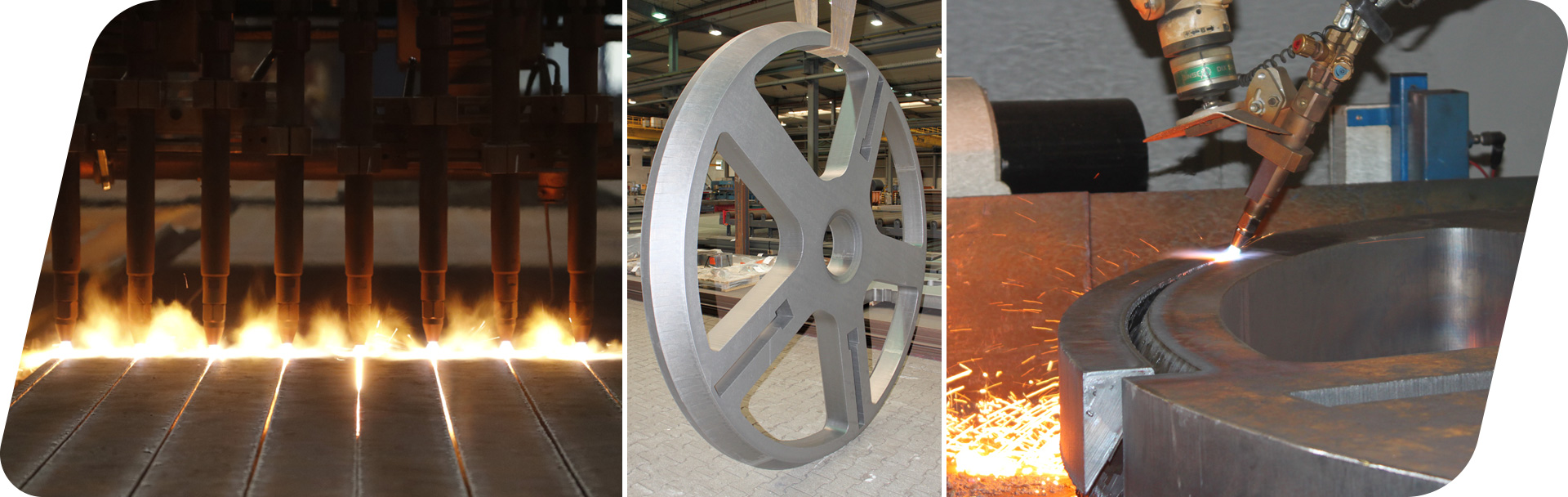
Autogenous flame cutting refers to a cutting process in which structural steel and metal sheets are separated by a flame. The combustion heat generated heats the material layers to ignition temperature so that the process continues autogenously through the subsequent layers. The cutting oxygen blows the resulting liquid slag through the joint. A flame cutter or flame cutting machine is used as a tool. In general, flame cutting refers to all cutting processes in which the material is burnt.
Oxy-fuel cutting systems
- Table sizes 6 x 30 m and 12 x 20 m
- Material thicknesses 10 – 300 mm
- Flame cutting systems with up to 12 machine torches
- Unit weight (starting material) maximum 28 t
- CNC-controlled torch carriage positioning
- Suitable for mirror-image cutting (e.g. for gear racks)
Oxyfuel cutting system for thick sheets (150-600 mm)
- Table size 4 x 8 m
- Unit weight (starting material) maximum 45 t
Strip burning system with 32 machine torches
- Material thicknesses: 8-60 mm, on request from 4 and up to 100 mm possible
- Smallest possible thickness/width combination: 40 x 6 mm and square from 40 x 40 mm, other combinations possible on request
- Lengths up to 12,000 mm
- Lowest possible deviation in straightness, i.e. little twisting or saberiness
Plasma cuts
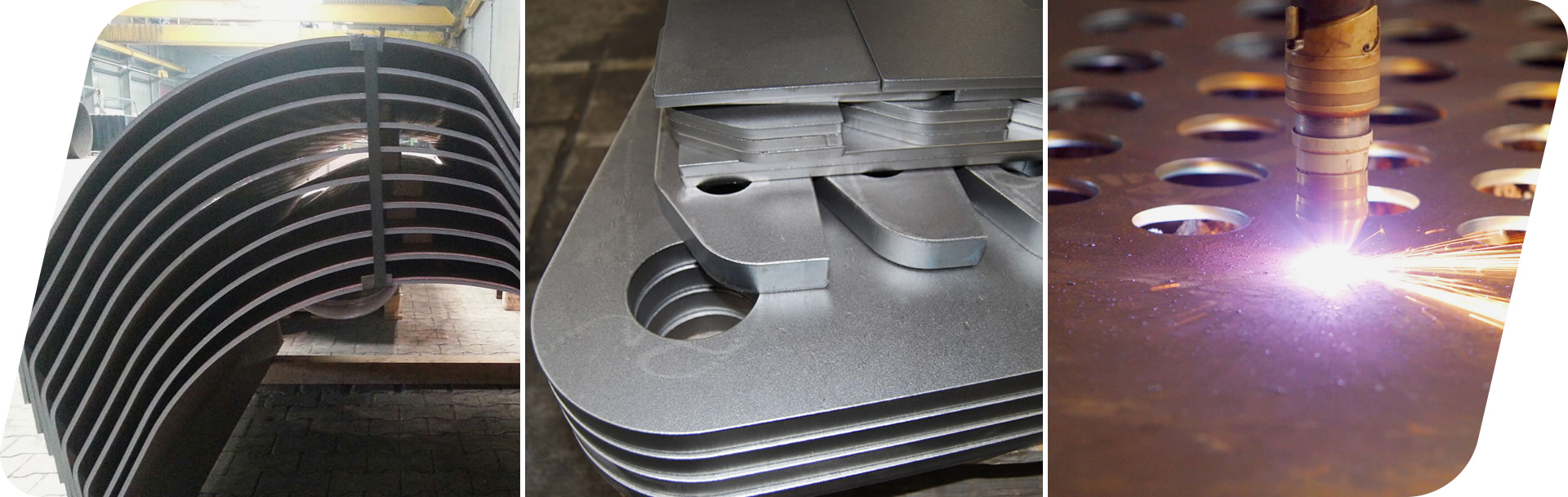
The plasma cutter generates an electric arc between the workpiece and an electrode. The plasma is an electrically conductive gas with a temperature of around 30,000 °C. The arc generates an energy density which melts the metal and is blown away by the gas jet. This is how the kerfs or plasma cuts are created. Inert gas mixtures that prevent oxidation are used to achieve an optimum kerf. For example, plasma cutting is used to create a rounded edge at an entry point.
CNC-controlled plasma cutting systems
- Table size 5 x 28 m
- Material thicknesses 4 – 25 mm
- Cutting systems with up to 2 machine torches
- Signing for the preparation of welded constructions or for forming
Laser cutting
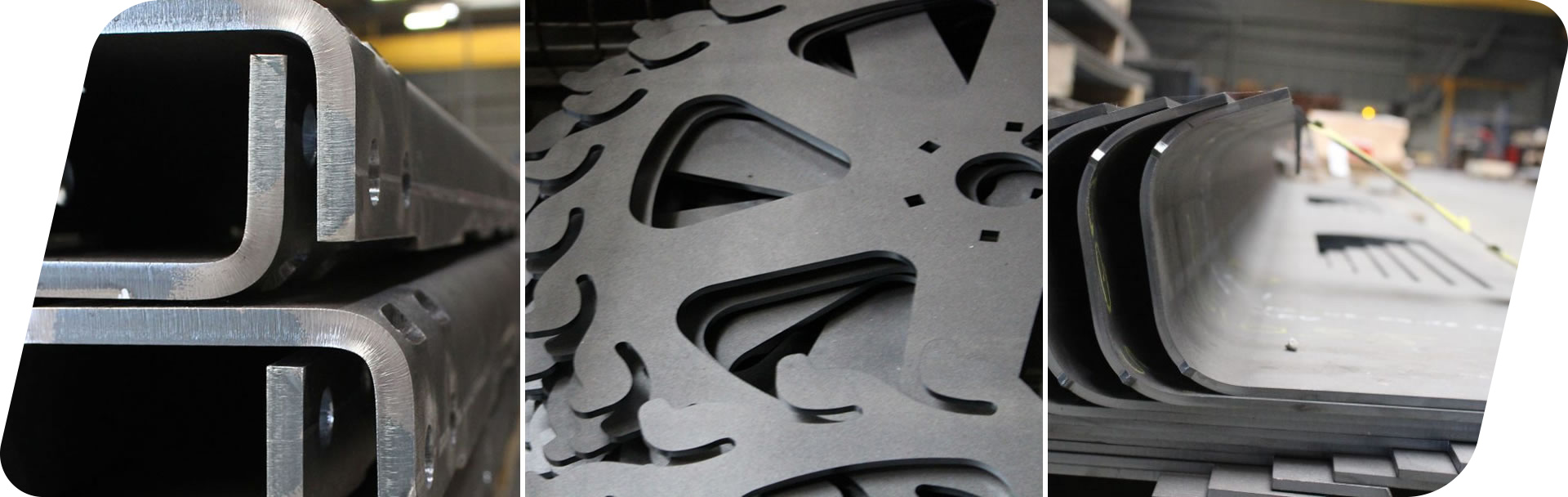
Laser cutting is also a thermal cutting process. When the laser beam hits the material surface, it heats the material to such an extent that it melts or completely vaporizes. The actual cutting process can only begin once the material has been penetrated by the laser beam. The system then traces the desired patterns. Depending on the job, the use of process gases can have a positive effect on the result.
Advantages of laser cutting
- Laser systems up to 12 kW
- Table sizes up to 3.5 x 14 m
- Material thicknesses of up to 25 mm (depending on the material quality)
- Small heat-affected zone
- No to minimal distortion due to heat
- Smallest tolerances possible (+/-0.1 mm)
Minimum angular deviation (max. 0.3 mm), tighter tolerances on request. Little to no reworking of the cutting contours.
Firing and laser tolerances
Firing tolerances in accordance with EN ISO 9013 or by arrangement
Preferred drawing formats for flame-cut parts
- .dxf
- .dwg
3D CAD
Unwinding and creating three-dimensional components of all kinds is part of our everyday work.
All common file formats, such as .step, .iges, .prt, .ipt, .sldprt etc., can be processed by us.
Weld seam preparation (chamfering)
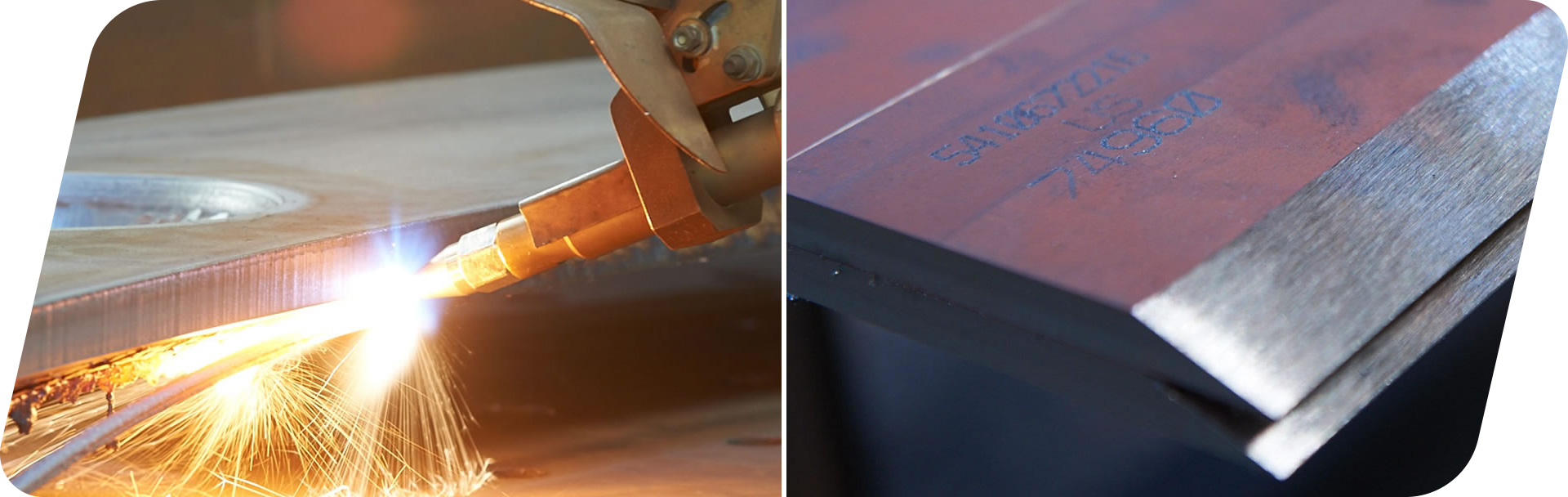
Mechanically inserted
Sanding units:
- Chamfering of 9 m per cycle
- Workpiece thickness up to 100 mm and workpiece width from 100 mm
- Setting without component rotation
- 85° top chamfer and 45° bottom chamfer
Welding edge former:
- No restriction due to component length
- Workpiece thickness up to 50 mm
Automated insertion
- 6-axis robot (chamfers in two planes and contours)
- Guaranteed repeat accuracy
- Chamfer cutting length up to 200 mm
Preheating
- Material-specific heat preparation for thermal cutting
- Gentle on the material thanks to a computer-controlled preheating process
- Energy-saving thanks to the use of the latest heating technology
- Logging of the entire process
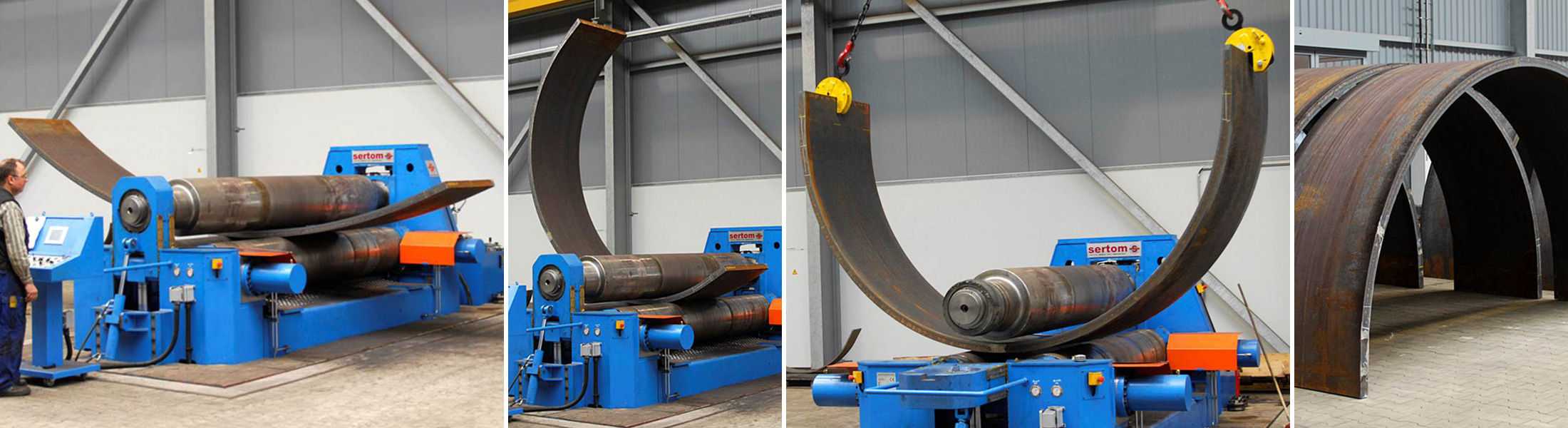
FAQ
Can I order flame-cut blanks online?
You can order flame-cut blanks from UnionStahl online. If you have any questions, please get in touch with our contact persons.
As a customer, do I have a personal contact person?
As a customer of UnionStahl Nord GmbH, you will of course have a personal contact person at your side who will assist you throughout the entire process. We look forward to hearing from you.